Services
Ultisoul works in collaboration with customers to identify their needs and provide customized services in following areas
- Calibration Services
- Local Support -Operations
- Lean Management
- Training and Development
- Facility Validation
- Project Management

Calibration Services
We are providing Calibration services On-site (Field) as well as Bench (Lab), as We understand the importance of downtime in terms of revenue.
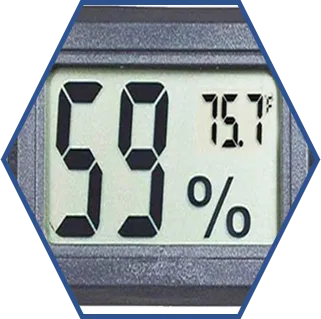
Thermal
Temperature sensors, Transmitters, Hydrometers, Humidity transmitters.
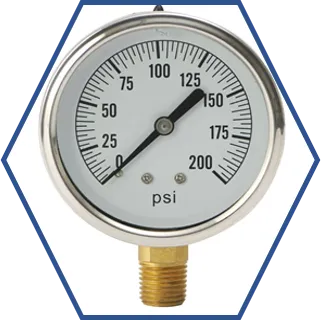
Pressure
Pressure Indicators, Transmitters, Dead Weight testers
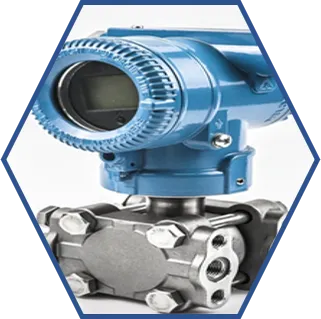
Flow
Gas/ Liquid meter/ Transmitters, Level sensors, transmitters
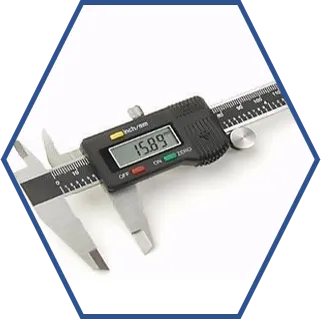
Dimensional
Calipers -Digital, Dial, Micrometers, Slip Gauges
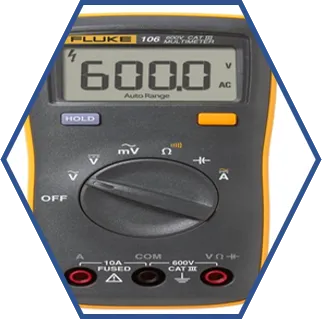
Electro Technica
Multimeters – Analog, 3 -1/2 Digital, LCR Meter, Megger, Insulation testers
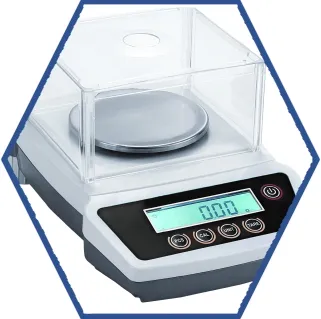
Weighing Balance
Upto 500 kgs., Torque Wrench, Tachometers, Lux Meter

Facility Validation
Facility validation for existing setup and we assist in setting up facilities to stay in compliance and Industry 4.0. We have validation experts who can help and guide from design qualification to process qualifications.
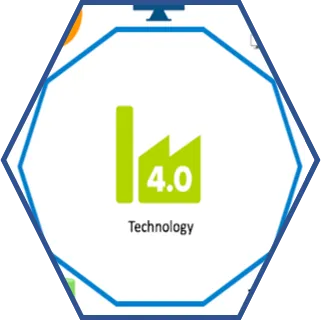
Industry 4.0
Loop Checking of instruments installed under 4.0.
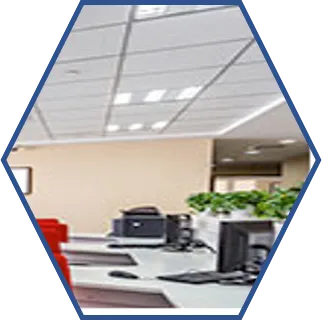
Illumination Validation
Workplace lighting standards
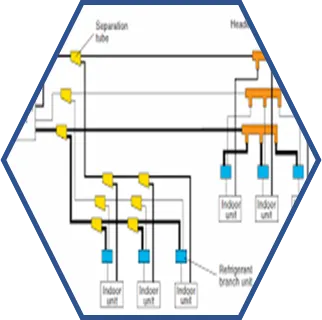
HVAC Validation
Following standards, guidelines and recommendations of ASHRAE , iSHARE and OSHA
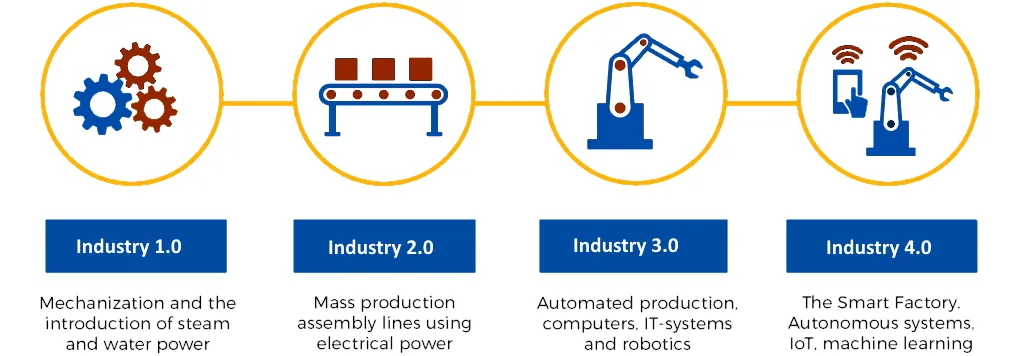

Lean Philosophy
Organization’s promoter worked on various popular Lean philosophies such as WCM, TPM, TQM, DBS, FBS and ABS. Team were responsible for creating a culture in the Organizations.
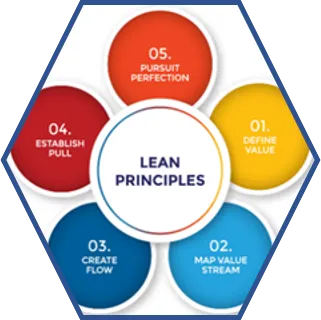
Lean
Creation of road map, conversion of lag to lead indicators through coaching and mentoring
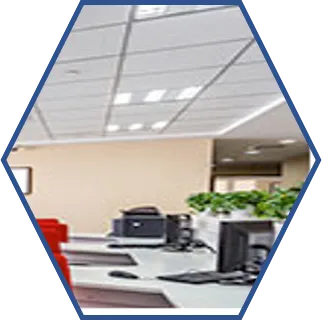
Local Support
Providing skilled Associates to work seamlessly at Customer end.
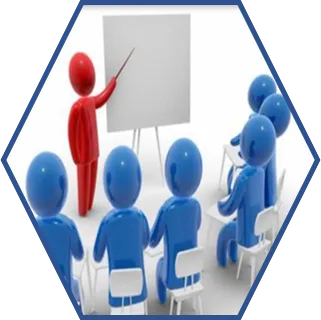
Trainings
Providing soft and hard skill training On-job as well as Classroom.

Project Management
Team is having great experience of greenfield as well as brownfield. In past, handled very large projects of manufacturing industries and Offices. Our Engineers closely monitor and coordinate with both Customer & execution team.
Monitoring on Cost Level
Monitoring on Schedule Level

Case Study
Drift Problem
Customer Profile
XYZ Ltd. Is engaged in manufacturing of injected Moulded components.
Business Situation
Injected Moulded components are used in high performance applications such as Aerospace, Medical etc. Dimensional accuracy of components is important and vital. Customer works on zero inspection policy of incoming parts. Customer is located overseas and all shipments are carried out through Air transport for various reasons such as size of consignment and OTD incentive. Customer is maintain high inventory truns. Customer penalizes heavily for any issues related to the component/parts. Since the Customer is in other continent any kind of rework also is very expensive.
Problem
Customer reported as issue with the dimensions of the received components. Customer asked XYZ Company to hold future shipments till the company submit a corrective action report of the issue. To find the root cause of the issue, XYZ company formed CFT ( Cross functional Team). This would also help the company to avoid future penalties.
Implication of the problem
Customer diverted the requirement to alternate supplier. XYZ company faces revenue loss as shipments are on hold and customer has penalized heavily.
Solution Description
CFT had carried out root cause analysis which included identifying the measurement instruments which were used for Mould preparation (setting of Mould) and final inspection. At final inspection, Air gauge comparator was used. The readings on Air gauge were noted by Operator and trend chart was plotted.
CFT found that the both instruments had valid Calibration stickers. Then CFT decided to verify the calibration report of both instruments. CFT found that both instrument’s calibration is done internally by the Quality function. During investigation CFT noted out the calibration details of the Calibrator. Found Quality function is not doing Calibration of Calibrator on regular basis, they were doing as on required basis.
CFT suggested for a third party inspection. Third Party submitted a report mentioning “ do not use” remark as Calibrator accuracy level had changed due to drift. Drift of Calibrator was ignored.
Regular Calibration of each measuring instrument is required to monitor the drift.
Benefits
Saved overall USD 7 M ( 5M Penalty + 2M revenue loss) by identifying the root cause

Case Study
Missing of Calibration Process
Customer Profile
UBL Ltd. Company engaged in manufacturing of large size valves.
Business Situation
UBL was involved in the assembly of large size different valves upto 1.5 Meter diameter. Different valves are used in Petroleum, Thermal, Steel, Water distribution etc. UBL has established world over for their quality, reliability and long life. Dimensional accuracy of valve is an important parameter as manufacturing cost is very high. Replacement of valve at field is exponentially expensive.
Problem
UBL faced fitment problem of supplied components from ABC Pvt. Ltd. UBL raised SCAR (Supplier Corrective Action Request) to ABC.
UBL was not happy because of Penalty and delay in shipment. UBL team decided to carry out supplier evaluation of ABC.
Root Cause
ABC company did not have a system of calibration, identification & traceability.
Solution Description
UBL decided to provide basic training on importance of Calibration and identification & traceability. UBL has changed the rating of ABC company and raised non-conformance which needed to be closed within 180 days.
Benefits
Saved losing the Business